Roman Concrete: Stronger, Self-healing, and Built to Last Forever
Roman concrete, often admired for its longevity and resilience, was revolutionary due to its unique blend of materials and its remarkable ability to withstand environmental stress over centuries.
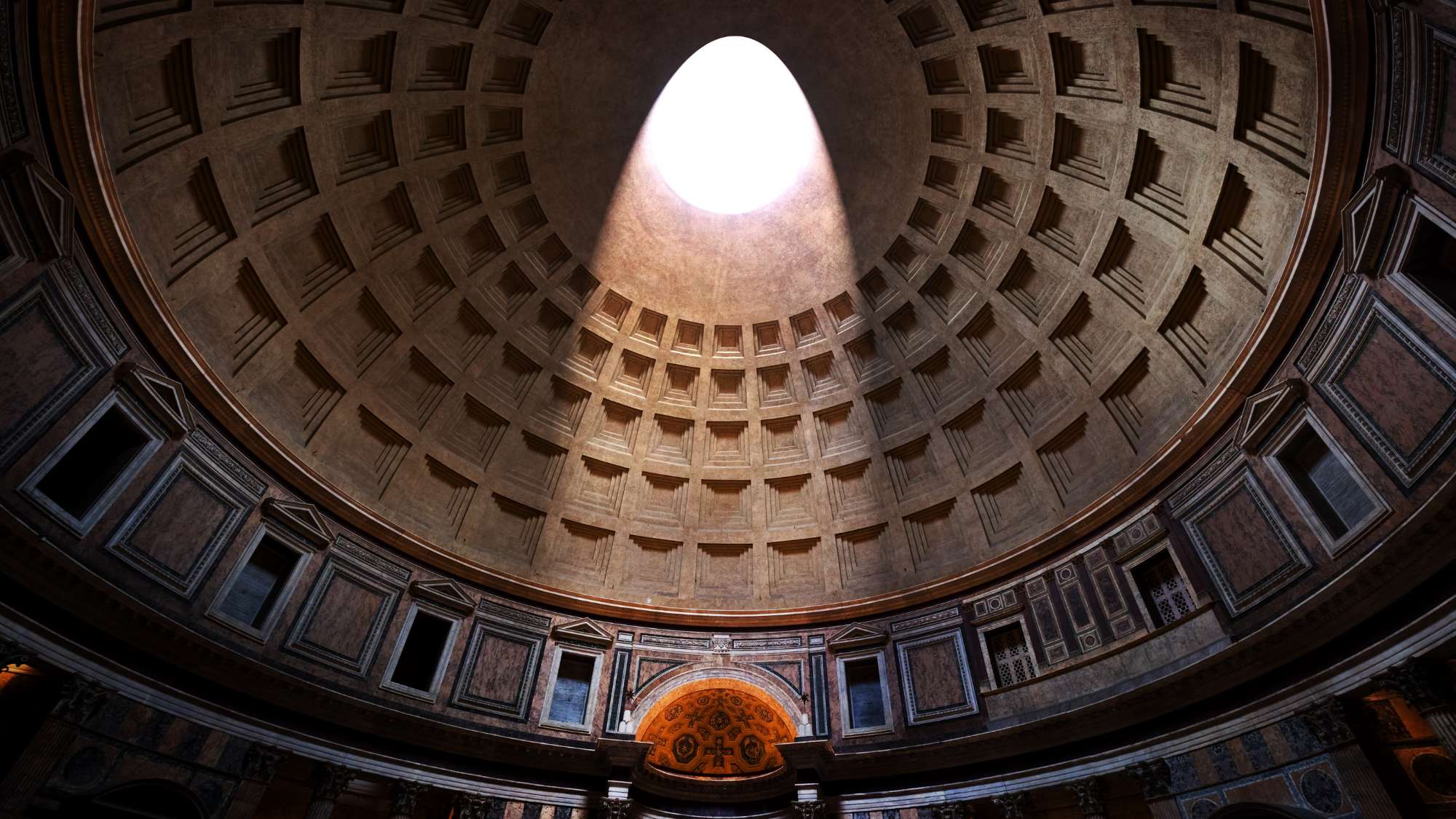
Romans have built impressive buildings and constructions that are still standing; two millennia later, we managed to find out how they were actually building their monuments and now, we are trying to replicate it.
The Secret Ingredient of Roman Concrete
In the first century BC, the Roman architect and engineer Vitruvius described a "powder" that achieved "wonderful" results when added to a simple lime-water mix. This "powder," made from volcanic tufts from the Campi Flegrei region near the Bay of Naples, enabled Roman mortars and concretes to set in seawater and create stronger structures than those built with lime cement alone.
The tufts, quarried near what is now Pozzuoli, were called pulvis puteolanis, or "dust of Puteoli," the Latin name for Pozzuoli. This gave rise to the modern term "pozzolana," now used for all cement additives that enable hydraulic setting.
"There is also a kind of powder which from natural causes produces astonishing results.
It is found in the neighborhood of Baiae and in the country belonging to towns round about Mt. Vesuvius.
This substance, when mixed with lime and rubble, not only lends strength to buildings of other kinds, but even when piers of it are constructed in the sea, they set hard under water."
Vitruvius
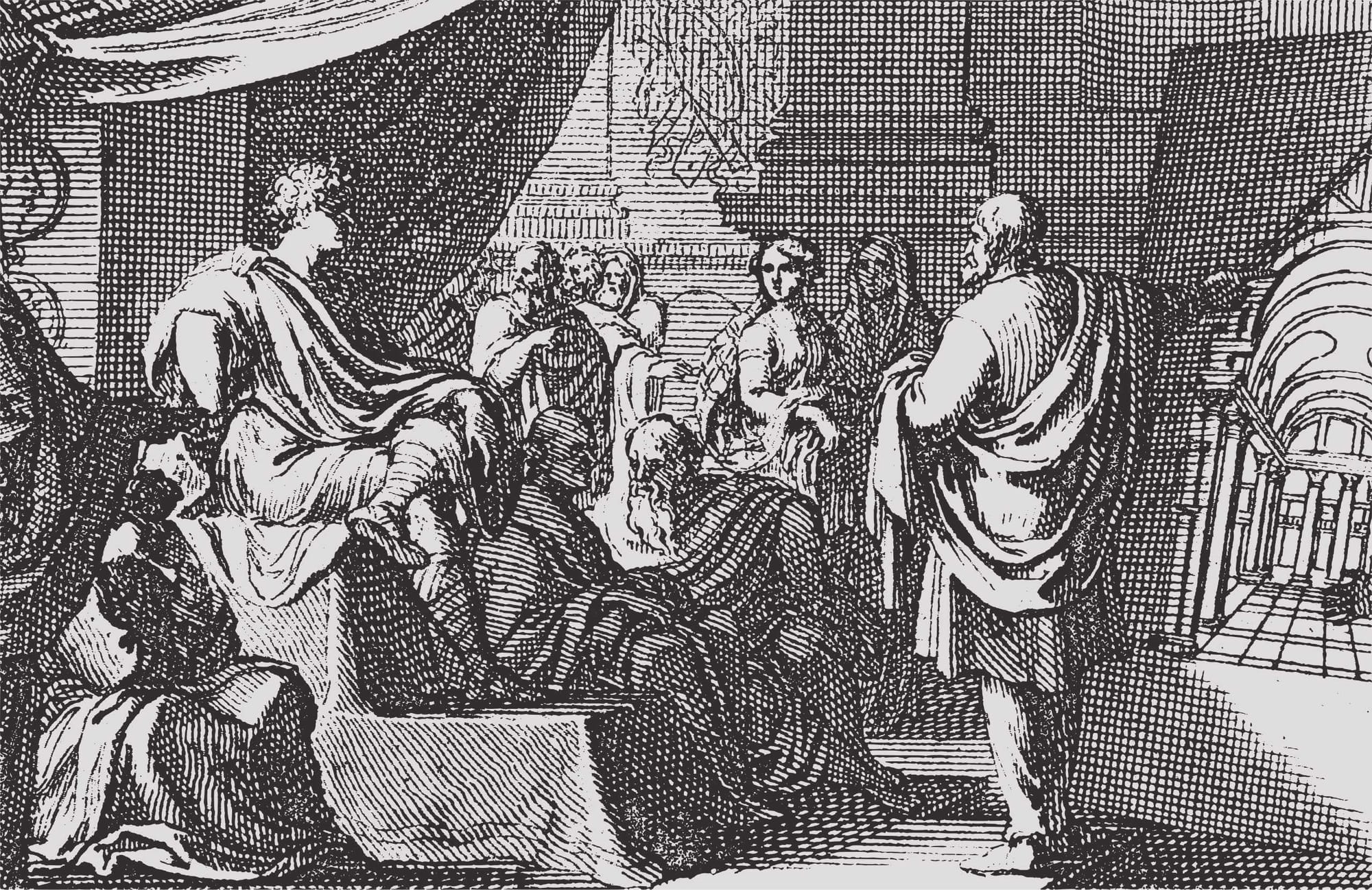
The Romans may have initially discovered the unique properties of this volcanic material while using local tufts, scoria, and lavas for constructing the harbor and port at Roman Puteoli, which later became a significant export. Vitruvius advised that:
"...the masonry which is to be in the sea must be constructed in this way.
Earthy material is to be brought from the district which runs from Cumae to the promontory of Sorrento, and mixed in the mortar, two parts of it to one of lime."
Despite their extensive use of these volcanic materials, the Romans likely had a limited understanding of the volcanic activity around the Vesuvius – Campi Flegrei region. They built heated saunas (sudatoria) in areas like Baiae and Puteoli using the naturally occurring hot springs (Vitruvius, De Architectura).
Until Vesuvius’s catastrophic eruption in AD 79, which destroyed Herculaneum and Pompeii, there is no evidence that Romans realized Vesuvius was an active volcano. Thus, they might be excused for believing the tufts around the Bay of Naples were unique in their origins and properties.
Although the Romans are often credited with inventing concrete, they were more accurately the first to develop its use in large-scale structures, such as vaults and domes. The technique of calcining limestone to create lime, which rehydrates to form a synthetic rock upon drying, has been known for around 9,000 years. Lime-cement materials date as far back as the Middle Eastern Pre-Pottery Neolithic B period, making limestone calcination one of humanity's earliest pyrotechnologies.
The Greeks also knew of concrete and mortar technology and used it routinely for floors, wall coverings, and waterproofing for cisterns, reservoirs, and baths from the Early Bronze Age. However, they rarely used concrete structurally, with one known example of a Hellenistic cast concrete barrel vault in Upper Peirene at Corinth.
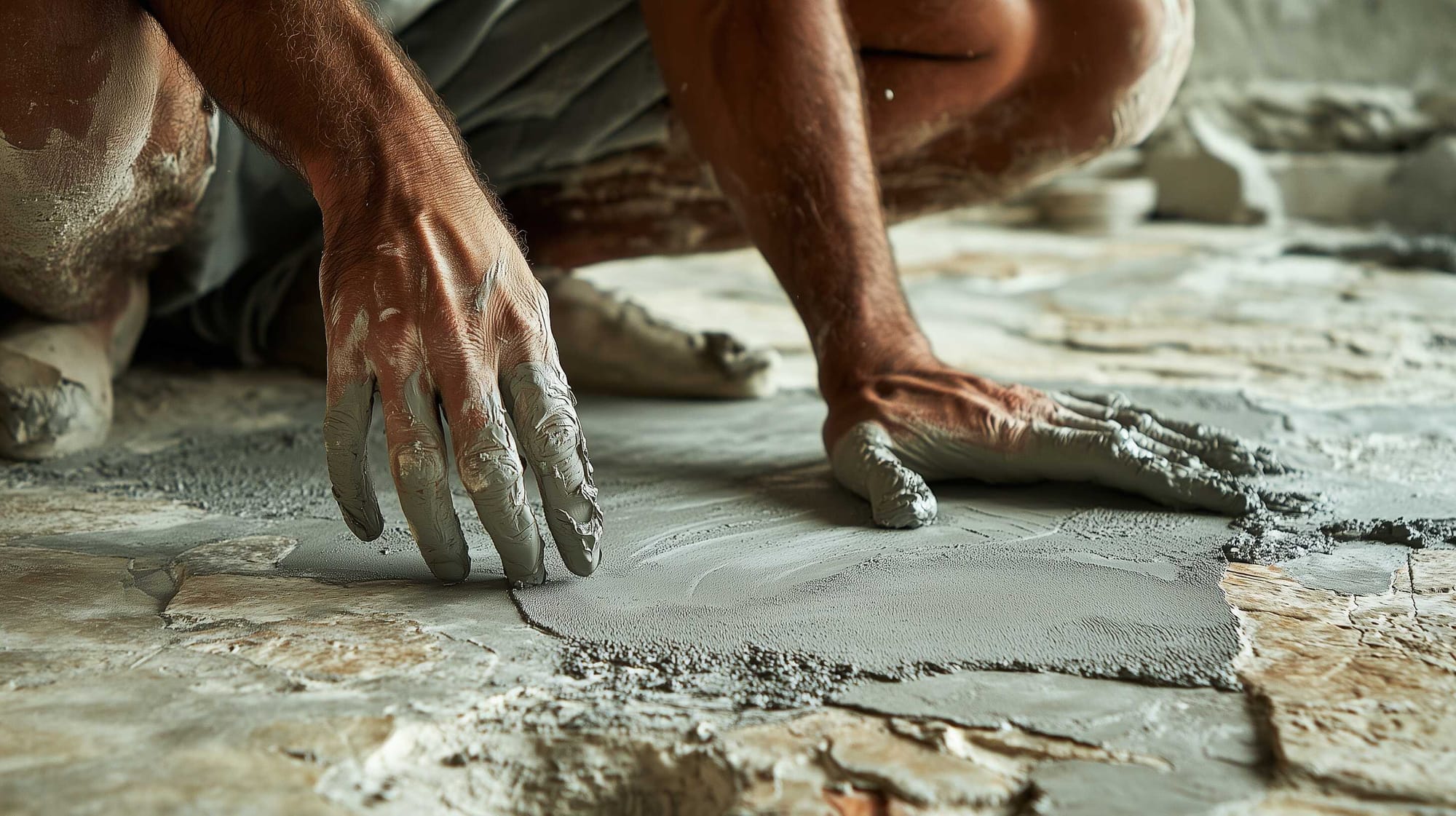
A Breakdown for Easier Understanding
Since some of the terminology might be quite complicated for the average reader, below you may find a brief explanation of each term, so you can become better acquainted with the subject.
- Mortar vs. Concrete: Both are mixes of slaked lime (a form of treated limestone) and an aggregate (which adds strength and bulk). The difference between mortar and concrete is in the size of the aggregate:
- Mortar has smaller particles (less than 5mm)
- Concrete has larger particles (more than 5mm)
- Plaster: It is similar to mortar but lacks any large aggregates, only very fine sand.
- Making Lime Cement: Lime cement is made by heating limestone to about 900°C in a kiln. This heating process removes carbon dioxide, leaving behind calcium oxide (quicklime). Ancient kilns, as described by Roman authors, burned materials like wood, olive kernels, and almond husks for days to reach the needed temperature.
- Why Volcanic Ash (Pozzolana) Works: Volcanic ash contains silica and alumina, which react with lime to create a strong, water-resistant cement. When lime and volcanic ash are mixed with water, they undergo a chemical reaction that binds the materials together, making a durable mortar or concrete.
- Chemical Reactions:
- Lime reacts with water to form a paste, which gradually absorbs carbon dioxide from the air, converting it back to a type of synthetic limestone.
- Adding volcanic ash promotes a "hydraulic set," which means the concrete hardens even underwater. This reaction produces a gel-like compound called C-S-H (calcium silicate hydrate) and other strong minerals, forming a highly durable, water-resistant material.
This unique composition explains why Roman concrete structures, like aqueducts and temples, have stood the test of time.
Mortar was essential for binding bricks or stones in Roman construction. Before the Roman period, mud brick and stone had already been widely used. Vitruvius detailed the requirements for quality dried brick, advising against sandy or pebbly clay because it would break down in rain, whereas “white and chalky or red clay, or even coarse-grained gravelly clay,” would make durable and lighter bricks.
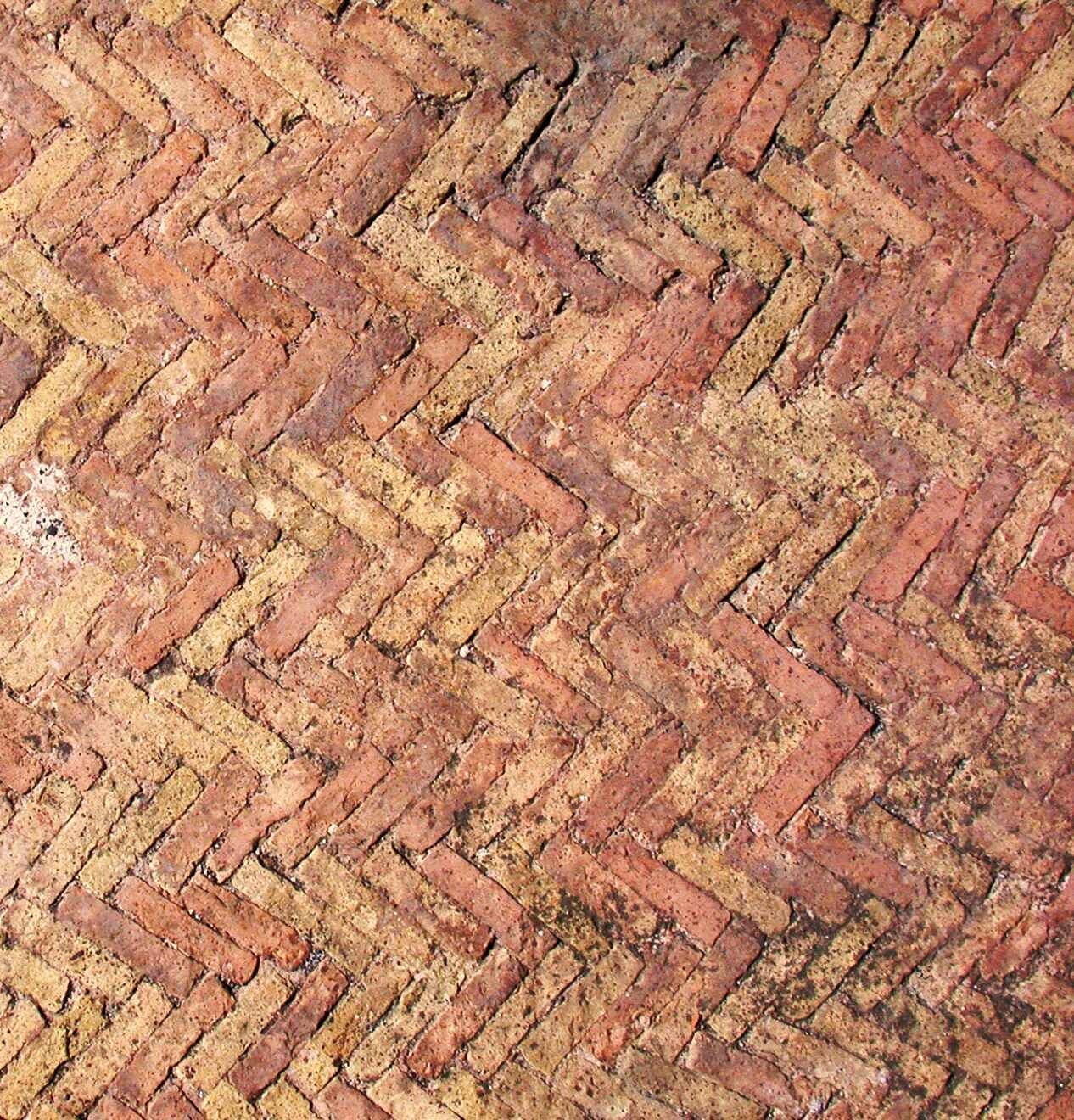
He recommended making bricks in spring or autumn and allowing them to dry for two years to prevent shrinkage.
Roman bricks floor in Trajan's Market in Rome. Credits: Theresa Knott, Public domain
While baked bricks were used in southern Italy, Vitruvius didn’t emphasize them, likely because of the high-quality stone available locally, such as volcanic tufa, limestone, and marble. He recommended testing stone for durability by exposing it for two years; weathered stone should be used only in foundations, while sound stone could be used structurally.
Vitruvius’ advice on material selection included:
- Using proven materials when possible,
- Testing new sources for durability,
- Prioritizing materials that are durable and economical,
- Ensuring quality sand for mortar, and
- Considering shrinkage in mortars and unbaked bricks.
Roman masonry methods offered significant advantages over large stone block construction, which required heavy labor and transportation of massive stones. Masonry, by contrast, was faster. Roman techniques, material standardization, and site planning accelerated construction—evident in projects like the Pantheon, completed in under a decade.
Roman construction was groundbreaking in its use of concrete, initially employed as a sturdy mortar in foundations and residential blocks. The careful selection of aggregates in concrete mixes was key, as the innovation and application of various compositions and strengths stand as some of Rome’s most significant contributions to building techniques. Skilled workmanship played an important role, with materials like tufa, peperino, and broken brick layered efficiently to enhance strength.
The Pantheon’s durability can be attributed to the high quality of mortar in its concrete mix, along with the meticulous selection and grading of aggregates. Roman concrete was characterized by low cement content, minimal water, slow strength gains, and minimal shrinkage.
Methods like opus caementicium used a core of rubble and mortar with stone facings, evolving into styles like opus incertum and opus reticulatum to improve both structural integrity and appearance. Vitruvius noted challenges in early masonry, including porous stones that absorbed too much water from the mortar, weakening it, and poorly bonded rubble cores, as seen in some Pompeian walls bound with clay instead of mortar.
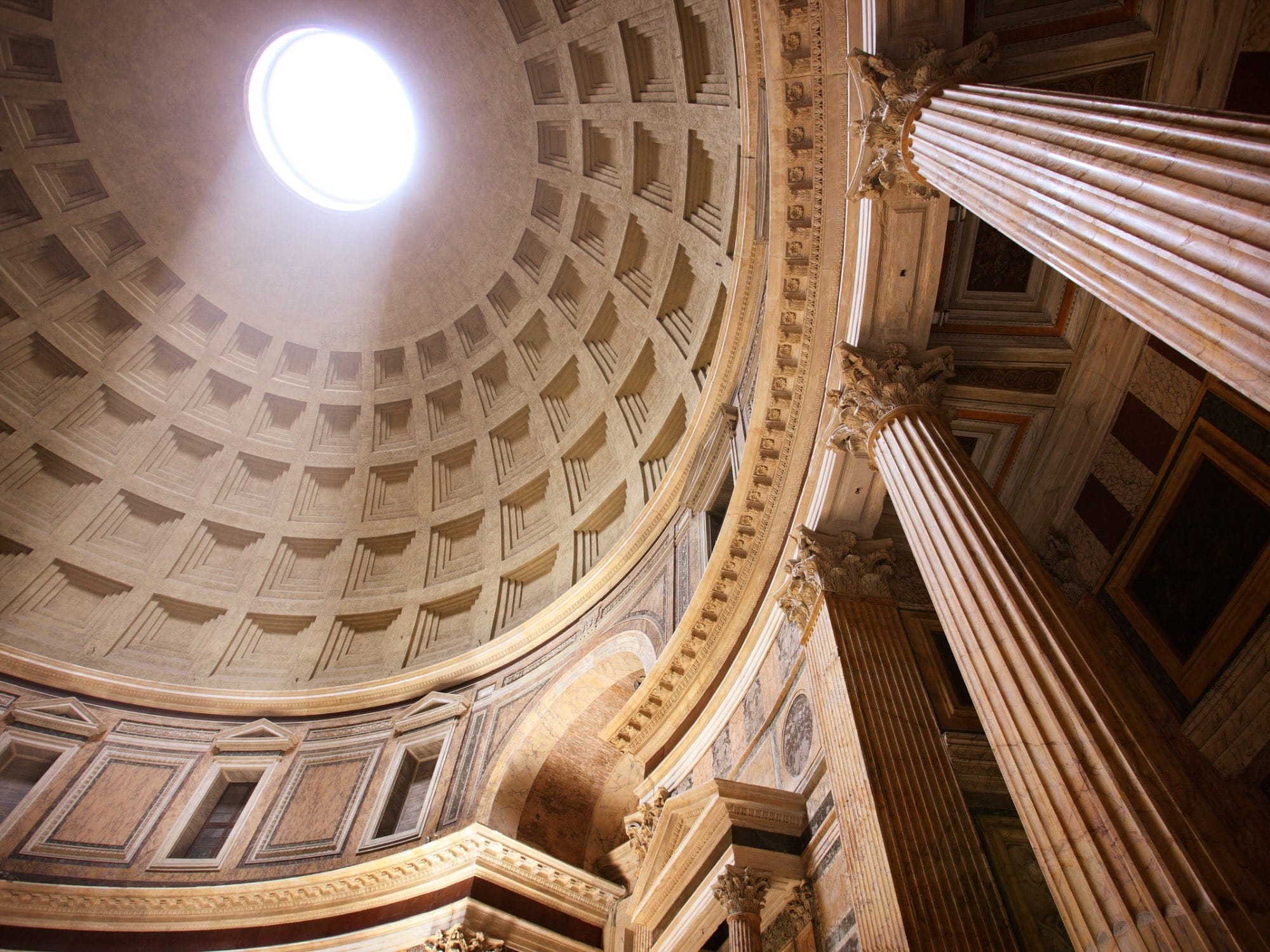
What was the Pozzolana?
A "pozzolana" is a siliceous or aluminous material that, in the presence of water, reacts with lime to create cement-like compounds. Pozzolanas include fired clays (as fresh clays absorb too much water, causing cracks) and various other materials like blast furnace waste or rice husk ash. Natural pozzolanas typically come from volcanic products.
The term "pozzolan" or "pozzolana" originates from Pozzuoli, a town north of Naples, where significant deposits of this material were found. It is believed that the Romans began using pozzolana around the third century B.C. This material enabled the construction of the impressive vaults and domes over public baths and proved invaluable for building bridge piers and harbor structures.
Pozzolana deposits were also located in the Alban Hills, south of Rome. Historically, the Greeks had probably used similar materials up to two centuries before the Romans, since there are studies that show they were using highly siliceous volcanic material known as Santorini earth. (Lessons from Roman Cement and Concrete, by Norbert J. Delatte Cleveland State University)
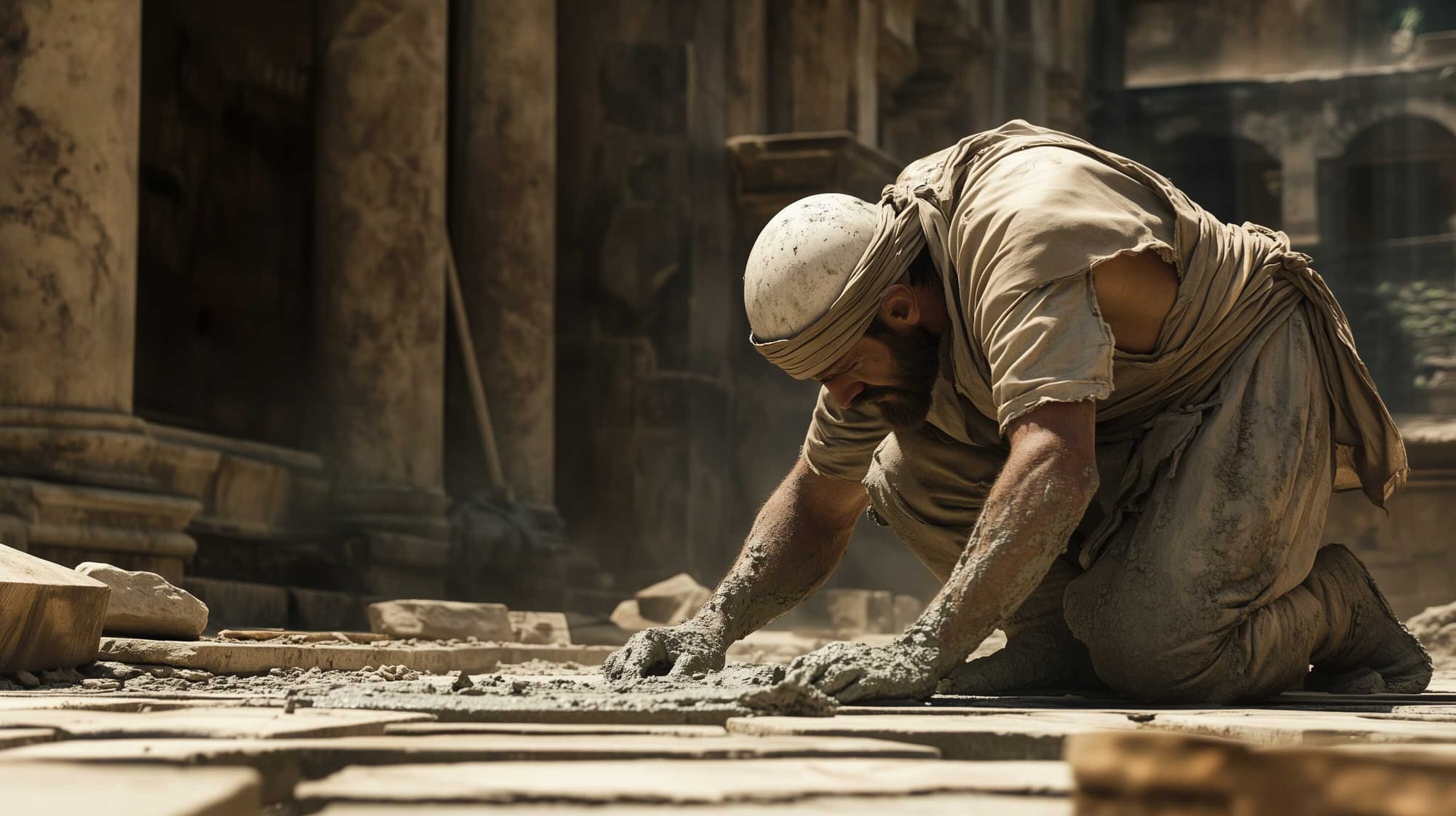
There is some debate about whether the Ancient Greeks used pozzolanas with lime cement specifically for waterproofing, though they had access to volcanic sources like Santorini and Melos. The Greeks most likely knew the properties of lime cement and primarily used it for waterproofing baths, cisterns, and floors.
More research is needed to determine if they intentionally used pozzolana in their early constructions. In Hellenistic Corinth, waterproofing involved "burnishing," or rubbing the mortar with stones to form a hard layer, though chemical tests of ancient plaster reveal a high silica content, possibly from volcanic materials.
The Romans likely adopted cement-making techniques from the Greeks but refined the use of pozzolanas and other aggregates, making their concrete more versatile and effective. This led to an "architectural revolution" where Romans excelled in using lime-based mortars and concrete, and they are often (though inaccurately) credited with inventing concrete.
Vitruvius mentioned a "powder" with "wonderful results" found around Baiae and Mount Vesuvius, likely due to the area's volcanic heat. Later studies describe the volcanic Campi Flegrei Caldera and nearby Quaternary volcanic areas (Ischia, Vesuvius, and Procida) that provided the Romans with pulvis Puteoli, or volcanic ash, to produce their hydraulic concrete.
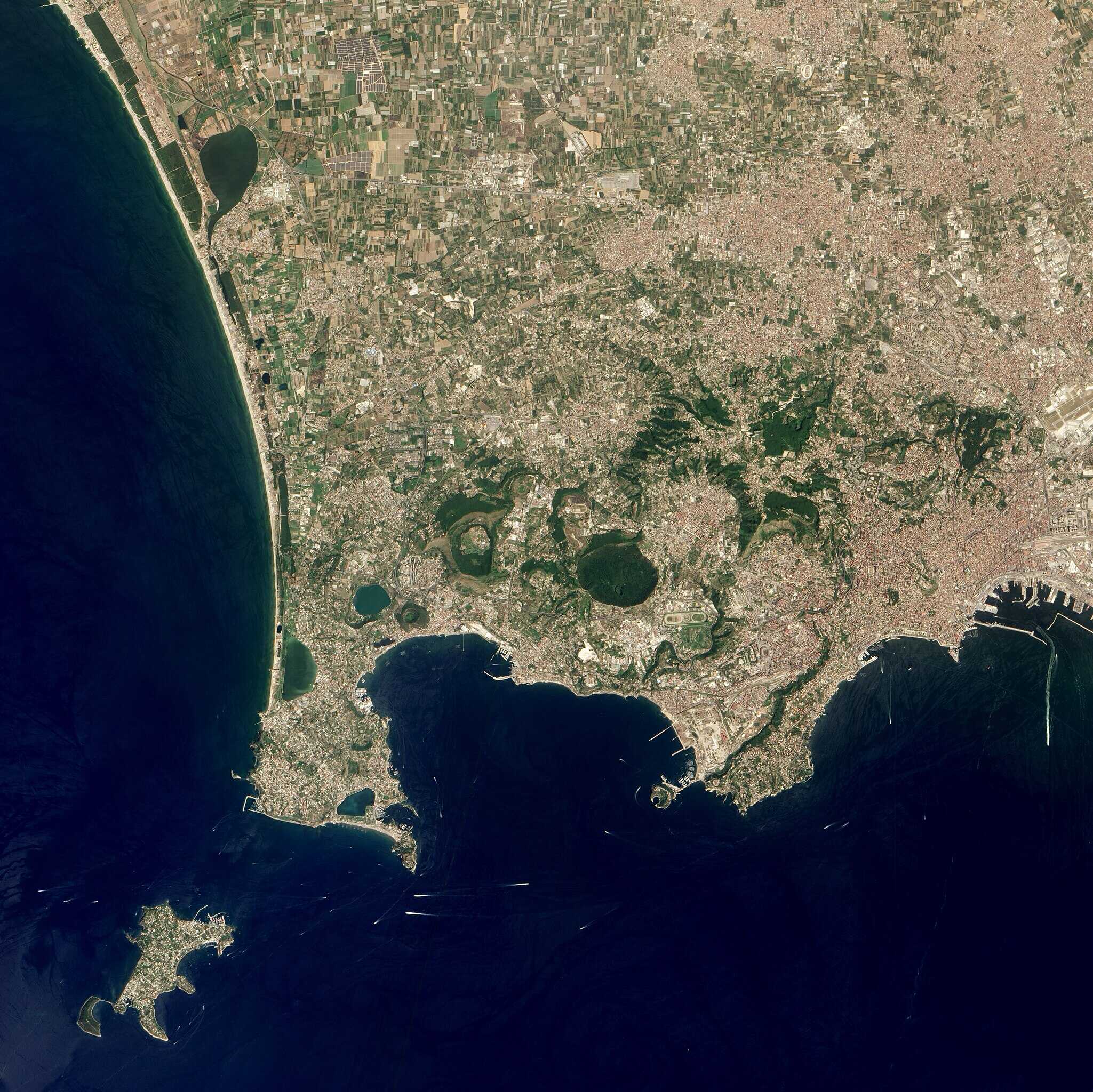
Roman projects along the Tyrrhenian coast, rich in volcanic ash and scoria, extensively used pozzolana from local sources.
The Campi Flegrei caldera cluster in the Bay of Naples. Credits: NASA, Public domain
Roman engineers might have been inspired by natural beach rocks that bound scoria with calcite, accidentally discovering that lime-pozzolana cement could set underwater. Without modern testing, they may not have realized that underwater curing actually improved concrete strength, as they did not apply water curing to terrestrial structures. The Pantheon dome, for example, used lightweight volcanic pumice in its upper sections to balance strength and weight.
Roman concrete is often associated with pozzolana, leading to the idea that pozzolana defines "Roman" concrete. However, in regions without volcanic ash, Romans adapted by using local materials and sometimes synthetic pozzolana, like crushed pottery, to waterproof baths, cisterns, and aqueducts. Roman structures in Germany used the local volcanic "trass" in areas like Cologne but not in Trier. Studies of Roman buildings in the Athenian Agora and Corinth show no volcanic pozzolana, even in aqueducts like Hadrian's Aqueduct.
For marine structures, however, hydraulic concrete made with lime and pozzolana was essential. Imperial Roman ports like Cosa, Ostia, and Puteoli used local volcanic pozzolanas, while Roman provinces without nearby volcanic sources had to import these materials to achieve the required hydraulic set. (The use of volcaniclastic material in Roman hydraulic concretes: a brief review, by Ruth Siddall, Department of Geological Sciences, University College London)
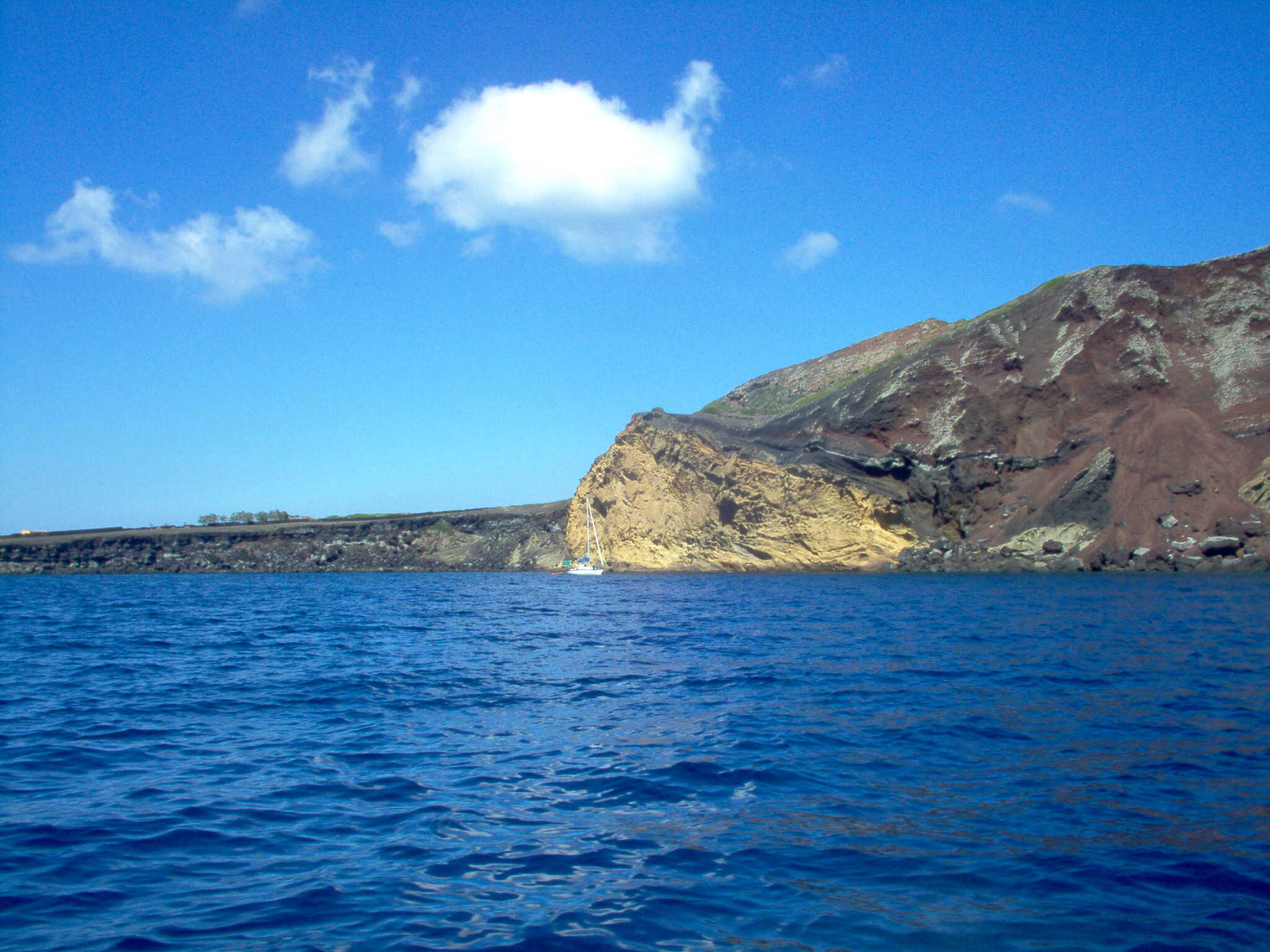
Roman Concrete: Designed for Timelessness
The Pantheon in Rome, with its remarkable 43.4-meter concrete dome built around 118–125 A.D., has stood for nearly two thousand years with only minimal repairs. Despite damage from a fire during Emperor Trajan’s reign and later removal of tiles, marble facings, and bronze roof girders, the structure remains in use today.
Roman concrete has proven more resilient than many other materials, as the internal concrete cores of walls, columns, and slabs have survived through time, while external facades of marble or stone have often eroded away. Concrete was essential to Roman infrastructure, offering a reliable waterproof material that hardened into a synthetic rock as tough as natural stone.
Samples of Roman concrete from ancient buildings and conduits have been found to be harder than many natural rocks. When Vitruvius wrote his architectural treatises in the first century B.C., he emphasized that while most buildings were expected to last around 80 years, careful construction could extend their lifespan significantly. At that time, concrete was still a new technology and used cautiously.
The earliest known concrete structure dates to about 121 B.C. and was of relatively poor quality, but later Roman structures were far more durable. Many of these enduring structures were later documented and illustrated in detail in architectural studies from the Renaissance, and recent studies showcase that Roman concrete had self-healing properties, capable of mending internal cracks when water (especially seawater) sipped through them, and strengthening to withstanding wear.
The foundations of Roman structures were crucial, and rubble masonry bound with lime mortar was used not only in masonry buildings but also in stone block constructions. Typically, the foundations were made half as wide again as the walls, though occasionally wooden piles were driven into the ground for extra support.
A key difference between modern ready-mix concrete and Roman concrete lies in the method: the Romans mixed mortar and aggregates directly on-site, compacting it within a framework. This type of construction often required scaffolding. Sometimes, free-standing scaffolding was used, while in other cases, logs were inserted into wall sockets and later removed.
The Romans developed a system using natural cement that significantly improved both construction quality and speed compared to previous methods. The Top-5 key aspects of this system included:
- Using formwork and scaffolding,
- Binding rubble with mortar made from volcanic earth,
- Carefully placing rubble within the mortar matrix,
- Incorporating recycled materials as rubble,
- Applying facing materials over a concrete rubble core.
Concrete became the foundation of life in Roman cities, supporting imperial infrastructure and commerce. With abundant resources like limestone and pozzolans for cement, along with armies of laborers, the Romans achieved concrete with a 2,000-year lifespan by enforcing strict quality standards across the empire.
Unlike earlier stone block methods that relied on metal clamps, Roman concrete was mostly unreinforced, although copper-reinforced concrete was used in at least one instance—the Baths of Caracalla in Rome.
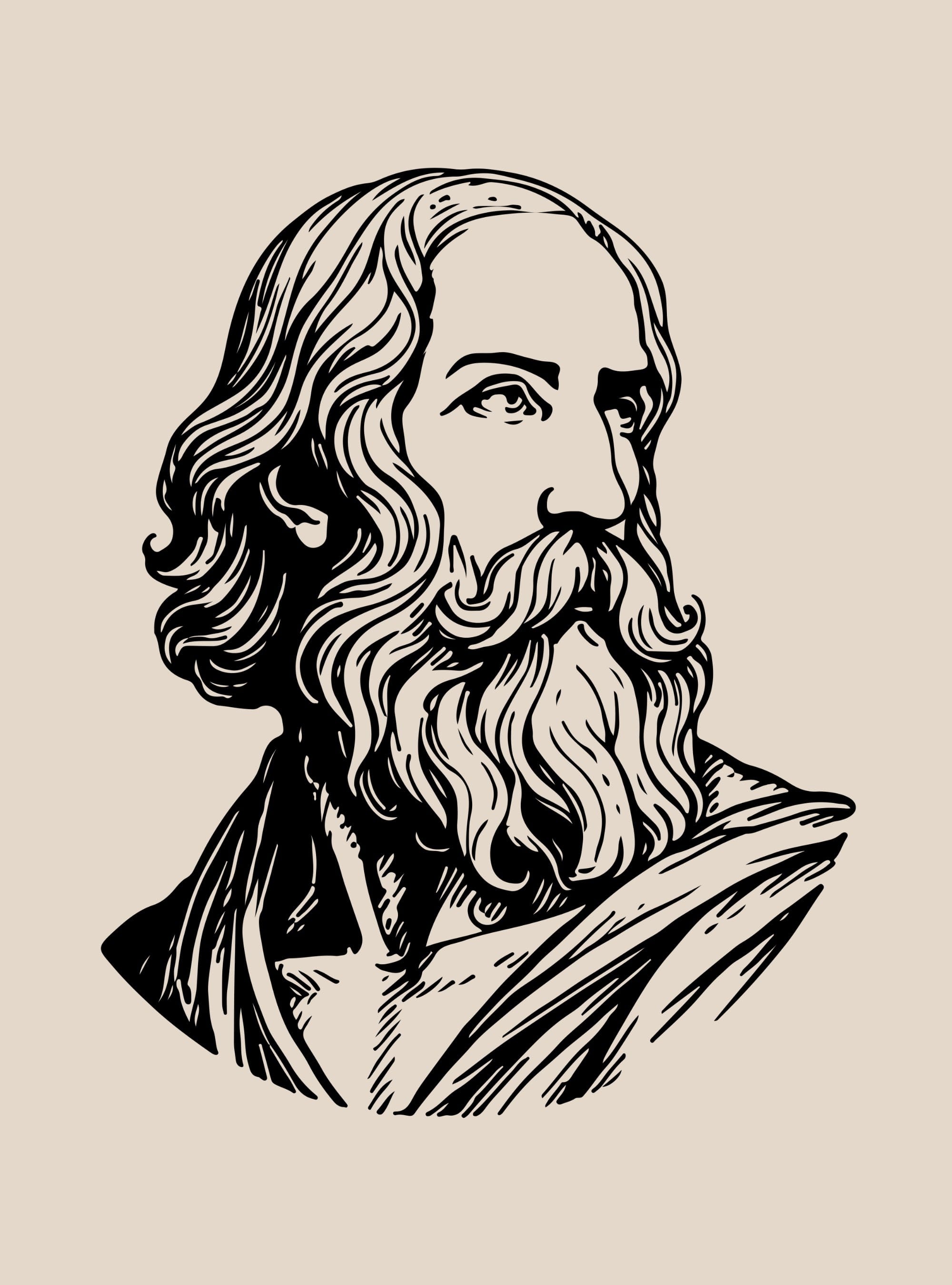
Vitruvius and other Roman builders emphasized several principles in construction:
A reliable building system combined with skilled workmanship ensures:
- Durable, cost-effective structures
- Proper grading and packing of aggregates result in stronger concrete
- Using recycled materials can reduce costs without sacrificing quality
- New methods should be introduced cautiously and refined over time
Thoughtful design, aligned with materials science and technology, leads to cost-effective, lasting structures. The Romans pioneered a construction system centered on cement and concrete, transforming building practices across the Mediterranean. Much of their knowledge and methods, still hold value in modern construction.
About the Roman Empire Times
See all the latest news for the Roman Empire, ancient Roman historical facts, anecdotes from Roman Times and stories from the Empire at romanempiretimes.com. Contact our newsroom to report an update or send your story, photos and videos. Follow RET on Google News, Flipboard and subscribe here to our daily email.
Follow the Roman Empire Times on social media: